Weiler House
San Francisco
Christopher Linton
Construction Management
Building Statistics
PROJECT // 01

Project team
Owner:
Confidential*
General Contractor:
Turner Construction
http://www.turnerconstruction.com/
Construction Manager:
Turner Construction
http://www.turnerconstruction.com/
Architects:
Marion Weiss and Michael Manfredi
Engineers:
Thornton Tomasetti (Structural Engineers)
http://www.thorntontomasetti.com/
Jaros, Baum & Bolles (M/E/P/FP)
Heintges (Glazing)
Renfro Design Group (Lighting)
General Building Data
Building Name ǀ Weiler House
Location and Site ǀ San Francisco, CA
Building Occupant Name ǀ Weiler Colocation House
Occupancy or Function Type ǀ Business/Assembly
Overall Building Size ǀ 188,603 SF
Number of Stories ǀ 6 stories above grade; 7 total levels
Primary Project Team ǀ Weiler House
Turner Construction, Weiss/Manfredi,
Tomasetti, Baum&Bolles(B&B), Heintges,
Renfro Design
Dates of Construction ǀ May 2015 – Summer 2017
Actual Cost Information ǀ Contract Value: Core and Shell - $100 Million
Project Delivery Method ǀ Design – Bid– Build
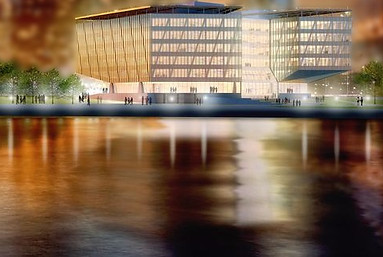
architecture
Design and Fuctional Components
This co-location center is designed to combine student research and companies in industry to create innovation in new products and technologies. The mixed use building contains a 2 story atrium located in the main entrance lobby shown in Figure 1. and a shaded slanted skylight . Allowing high natural daylight, low emissivity and a reduction in lighting operation. A centralized stairway is used to incorporate seating and natural egress to the second floor. Leading to tenant fit out spaces that surround the core elevator.
zoning
Utilizing group 6 (Commercial) and group 3 (Community Facility) zoning. The project has a zoning area of 188,603 SF which excludes the below grade level and the MEP chase on 1-6.

Figure 1. Interior Lobby
Applicable codes
2014 San Francisco Building Code
2014 San Francisco Fire Code
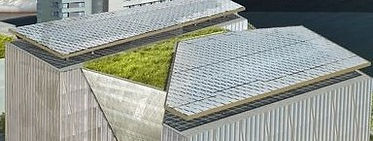
Figure 4. Green Roof System

